We provide engineering consulting services in the field of numerical simulation
related to the design, testing and product optimization.
Computational Fluid Dynamics and Finite Element Analysis
for Process and Equipment Design
Fluid forces, thermal effects and structural integrity can all impact performance of products and industrial processes.
Computational Fluid Dynamics ( CFD) and Finite Element Analysis ( FEA) allow a detailed understanding of fluid flow and mechanical response in real-world environments
TEASistemi is a leading specialist in the use of CFD and FEA techniques for process analysis and equipment design, also combining physics solvers for high fidelity multiphysics simulations (thermal fluid-structure interaction).
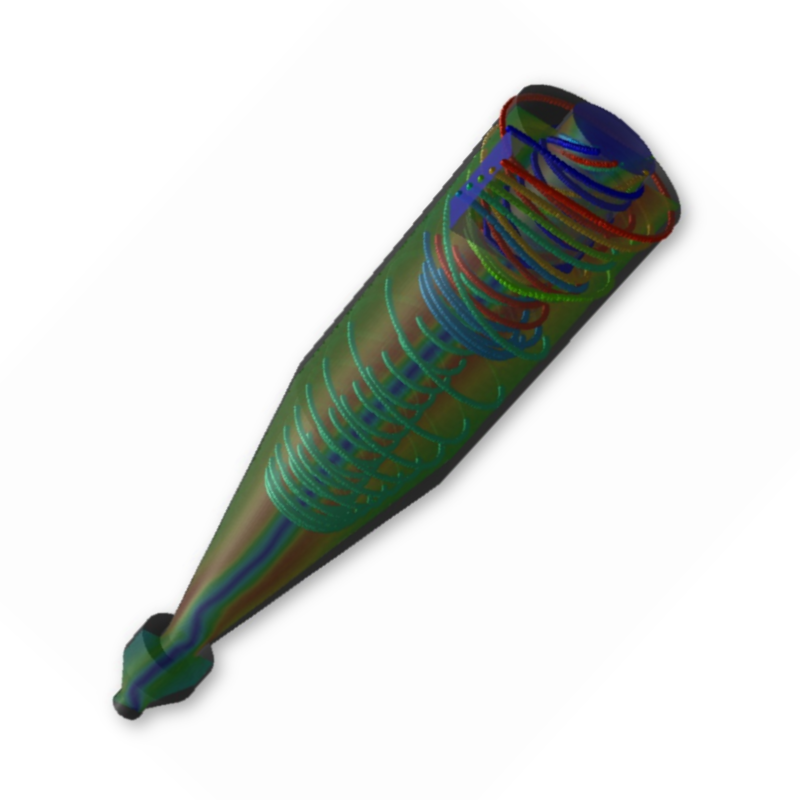
Software
We use the best computanional software available on the market in order to perform design activities and to meet Client's need
Among our main tools we cite ANSYS Fluent, ANSYS Mechanical, STAR-CCM+, OpenFOAM, SolidWorks.
Process Optimization
The behaviour of fluids in a process system directly impacts how efefctive that process is.
Computational Fluids Dynamics provides a detailed understanding of flow distribution, pressure losses, heat transfer, particulate seperation, collection efficiency, etc. in order to achieve efficient process and meet environmental regulations through better designs.
Design evaluation, verification and optimization
In the design of process equipment, Computational Fluid Dynamics is valuable to verify different equipment configurations, or to compare performances for different operating regimes.
In case of revamping or trouble-shooting, full-scale CFD models can be constructed to provide clear and comprehensive flow visualizations that help you get to the root cause of problems quickly, and to test alternative solutions efficiently, thus resulting in lower costs and shorter time to market.
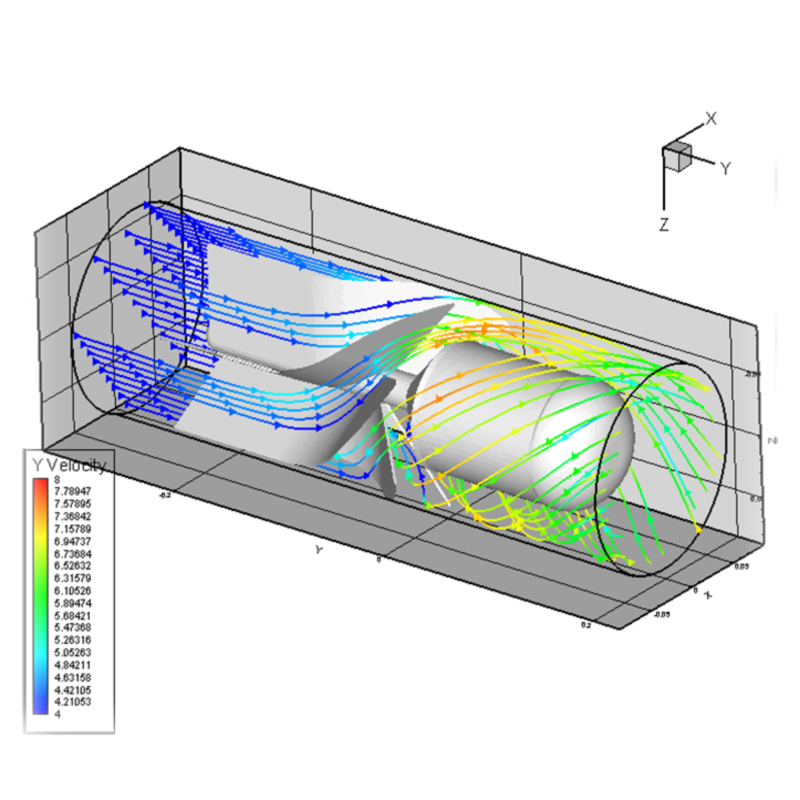
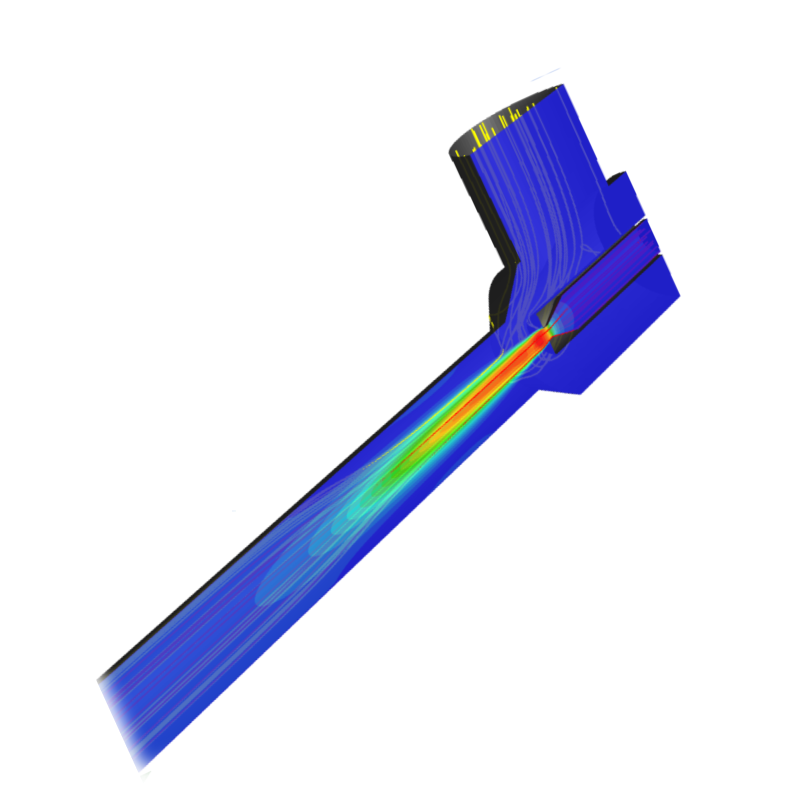
Stress analysis for Design Certification
According to ASME Section VII DIV 1 and PED directive, when rules for details of design and construction are note given in the Code, the Manufacturer shall provide design and construction details which will be safe as those provided by he rules of the Code.
Finite Element Analysis ( FEA) is often chosen as the tool as it is very powerful and relatively inexpensive.
Applications
- Filters
- Pipping Systems
- Gravity and Cyclonic Separators
- Multiphase Flow Meters
- Pumps
- Ejectors
- Mixing Devices
- Slug Catchers
- Heat Exchangers
- Valves
- Packed Columns
- Noise/Erosion issues
- FIV-AIV Analysis
RPN Refinery Plant Energy Recovery Project
Client: Serbian National Oil Company I Location: Serbia
NIS, the Serbian National Oil Company, was starting an overall bottleneck plan to increase performances and reduce operational costs of Pancevo Refinery Plant.
In particular, the main issue of the plant was the large consumption of gas to produce vapour required for process, and the large amount of energy lost in cooling exhaust vapour at process cycle. The use of this energy to reduce gas consumption, but without the installation of new facilities, was the principal goal to be reached by the project.
TEA has a specific experience in process development for energy saving applications, a deep knowledge of phenomena related to oil&gas processing, and an efficient working organization to provide just in time results at competitive price.
Since the project would require out-of-standard solutions to reach the project goal, TEASistemi was providing to the Client an added value in combining engineering capabilities to solve complex problems with research attitude to identify alternatives to unfeasible approaches in process design.
TEASISTEMI reached the project target within schedule trough a combined approach:
- On a side, a group of engineers was analysing the current solutions and their impact in terms of costs and final performances
- In parallel, a mixed group of engineers and university researchers was evaluating brand new approaches to maximize performances, with no-cost limitations
- Finally, all the solutions from abovementioned activities were ranked using a of cost-benefit financial model, and the one with maximum revenue along the time was selected for implementation
This approach has guaranteed the selection of a feasible technical solution with higher value-for-money, maximizing the financial indicators of Project balance
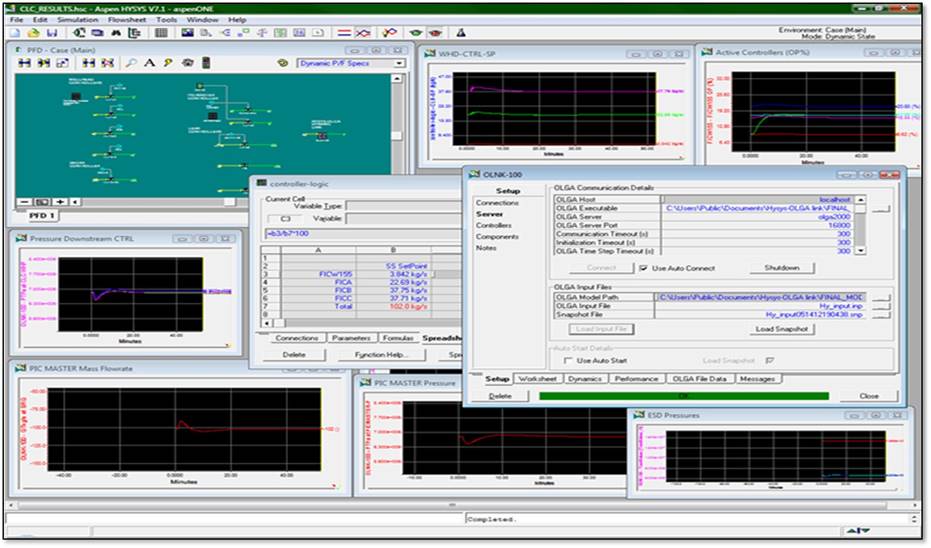